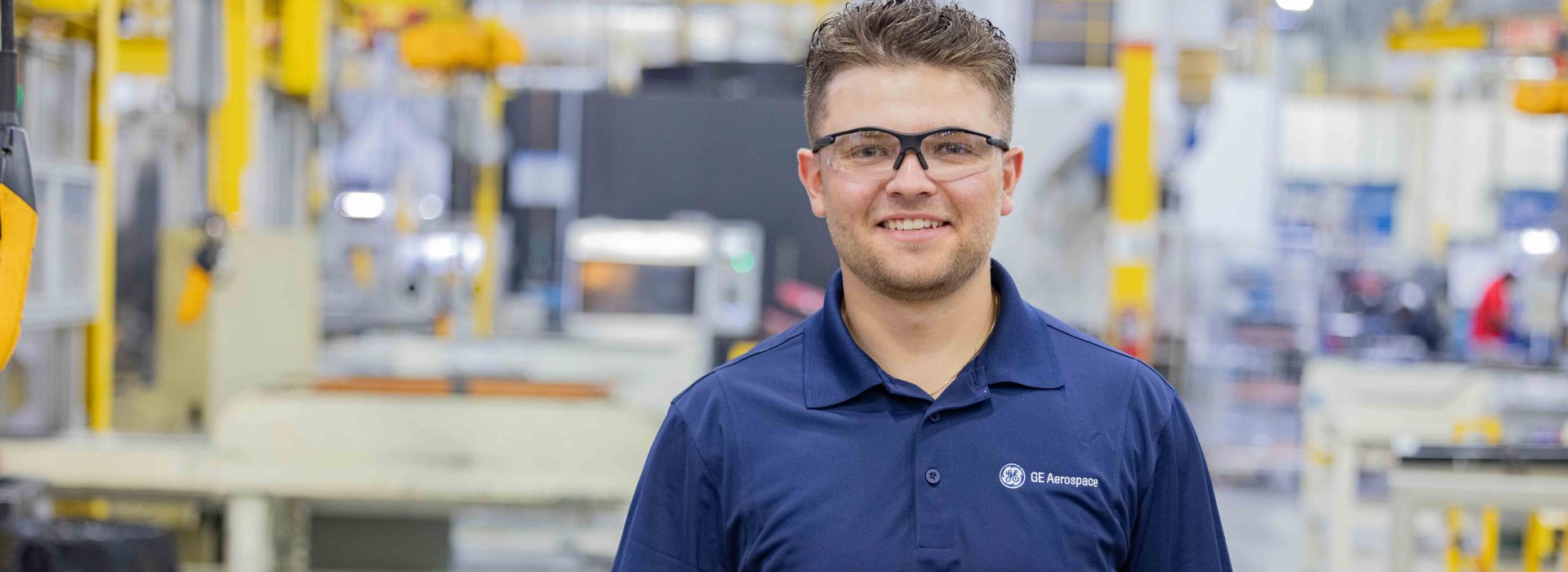
Facilities and Maintenance Rotational Program (FMRP)
GE Aerospace offers rotational assignments for facilities and maintenance, providing technical and leadership learning opportunities.
At GE Aerospace, we believe the world works better when it flies. We are a world-leading provider of jet engines, components, and integrated systems for commercial and military aircraft. Working at GE Aerospace means you are bringing your unique perspective, innovative spirit, drive, and curiosity to a collaborative and diverse team. It means that if you have ideas, we will listen. You will be able be a part of our LEAN transformation so that you can work smarter and not harder. Here, you will do work that you will be proud of. Work that really matters.
See your future take flight!
Selected candidates will complete three, 8-month rotations in the following areas:
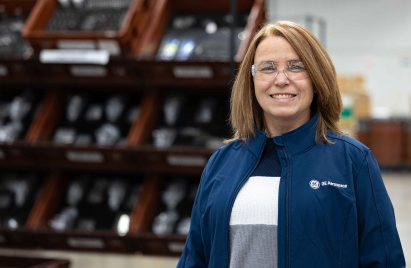
Lorem Ipsum
Facilities Management
- Supervise and coordinate scheduled maintenance, repair, shut down, and overhaul work.
- Influence the development of real estate strategy for the site, including project management and process improvement.
- Integration of energy/utility optimization in alignment with energy efficiency and sustainability.
- Collaborate cross functionally to ensure site compliance to local regulatory and corporate facilities standards.
- Support loss prevention & risk reduction priorities based on site profile.
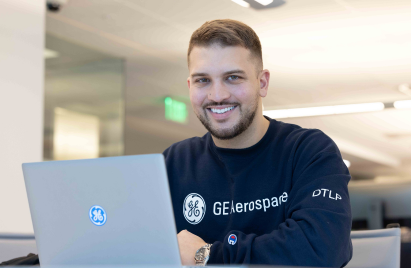
Lorem Ipsum
Maintenance Management
- Develop planning/scheduling standard work for preventive maintenance and corrective actions.
- Drive improvement in asset reliability and facilities. maintenance key performance indicators (KPI) metrics.
- Develop skills necessary to become a subject matter expert in Maximo Application Suite (MAS).
- Impact maintenance culture through development of standard operating procedures, master instructions and detailed job instructions.
- Outline strategies to mitigate unplanned machine downtime.
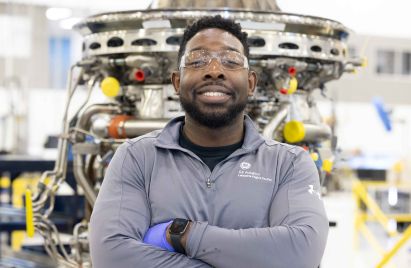
Lorem Ipsum
Total Preventative Maintenance
Implement and oversee Total Preventative Maintenance (TPM) Strategy based on asset criticality.
Track spare part and inventory usage to maintain spare part/inventory control.
Facilitate TPM events at immediate site and support other sites with similar install base.
Collaborate with operations to align operator preventative maintenance with asset standards.
Participation on a cross functional teams as part of Continuous Improvement efforts.
Track spare part and inventory usage to maintain spare part/inventory control.
Facilitate TPM events at immediate site and support other sites with similar install base.
Collaborate with operations to align operator preventative maintenance with asset standards.
Participation on a cross functional teams as part of Continuous Improvement efforts.
A sense of mutual respect and mindfulness permeates our culture-in fact, it’s the key to our success.
Lorem Ipsum has been the industry's standard dummy text
Lorem Ipsum has been the industry's standard dummy text ever since the 1500s, when an unknown printer took a galley of type and scrambled it to make a type specimen book.
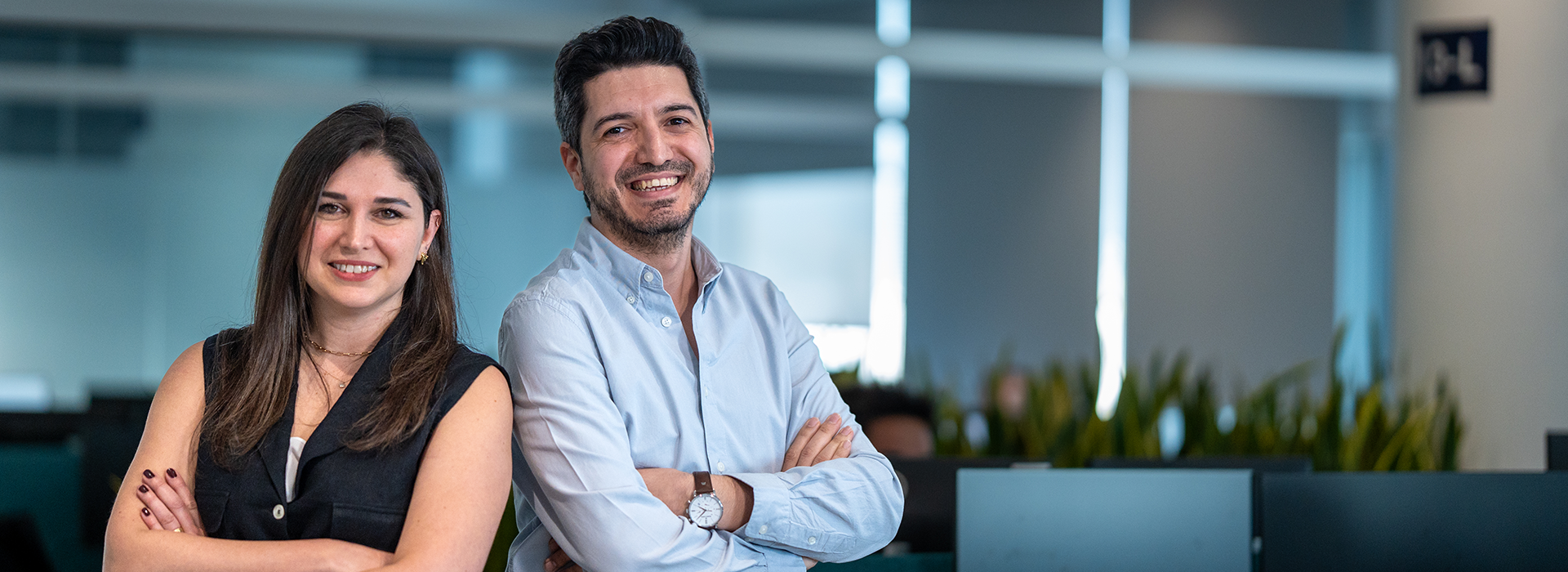
Lorem Ipsum
Join our talent community.
Receive up-to-the-minute job openings tailored just for you
A sense of mutual respect and mindfulness permeates our culture-in fact, it’s the key to our success.